Is it Difficult to Build a Kit Car? What You Need to Know
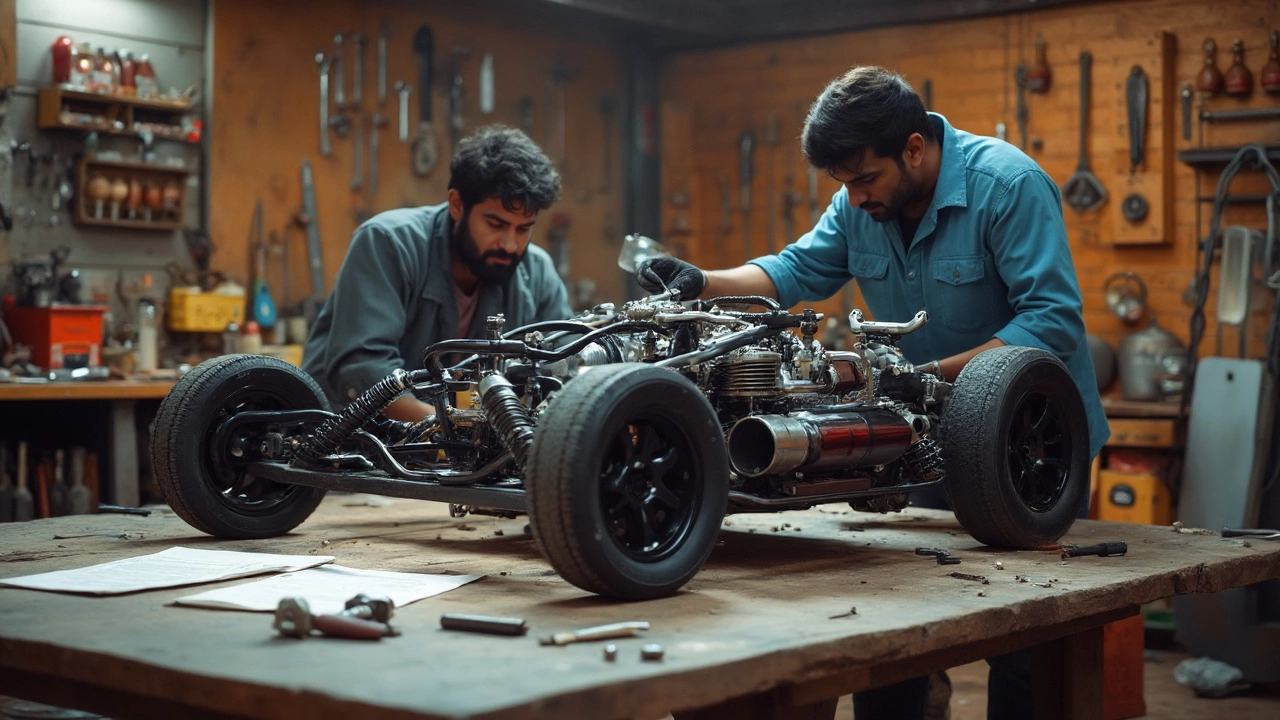
Think building a kit car is just snapping pieces together like Lego? Not quite. There’s real work—cutting, drilling, sweating, sometimes cursing—waiting for you once those boxes hit your driveway. Most kits today give you solid instructions, but they expect you to know your way around a toolbox. You’ll deal with everything from lining up panels so they fit right, to figuring out wiring if the harness looks like spaghetti.
If you already like wrenching on your ride—doing brakes, swapping a stereo, or fixing small stuff—you’ve got a head start. But kit car building has its own curveballs. Sometimes you’ll wrestle with bolts that just don’t want to line up, or chase leaks where you least expect them. A basic kit can take 250 hours or more. Some people stretch it out for years, just working weekends when they feel like it. The biggest shock for beginners? It’s not always cheaper than buying used; costs like paint, donor parts, and random tools really add up. But if you’re after a one-of-a-kind machine, with your fingerprints on every inch, few things beat that last day when you finally fire up your build and roll it out of the garage.
- What Is a Kit Car Build Like?
- Tools, Skills, and Setup You Really Need
- Speed Bumps: Common Problems and How to Dodge Them
- Tips to Make the Job Way Easier
What Is a Kit Car Build Like?
So, what’s it actually like to build a kit car? Here’s the honest truth: it’s a lot more than just opening some boxes and screwing stuff together. Most kit cars arrive as a main chassis, a pile of body panels, hardware bags, and a thick manual. Some kits expect you to use major parts from a donor car, like an old Mazda MX-5 or a Ford Mustang. Others provide everything but the engine and transmission, leaving you to hunt down the oily bits from pick-n-pull or online.
The first days feel awesome—lots of unpacking, organizing, and dreaming. But once you start, you’ll find each stage is its own adventure. You might spend hours just test-fitting body panels or fabricating tiny brackets because factory holes don’t always line up. Building one feels a bit like restoring an old classic, but with more guesswork and way more calls to tech support.
You’ll often need to:
- Prep the donor parts—cleaning, repairing, sometimes rebuilding them
- Mock up the chassis and bodywork before you even start tightening bolts
- Run wiring for the lights, fuel system, and dash (plan for extra coffee and patience here)
- Troubleshoot weird fitment issues you don’t see in the YouTube videos
One experienced builder put it best:
“Finishing a kit car is less about your mechanical skills and more about your stubbornness. Every build hits weird problems. You fix one thing, two more show up. But when it starts up for the first time, it feels like nothing else.” — Wayne G. Dempsey, author of '101 Projects for Your Kit Car.'
Don’t expect kit car building to go fast if you’re working in your home garage. A 2023 survey by Kit Car Magazine found most amateur builders take from six months to two years, working nights and weekends. Here’s what typical project timelines look like:
Stage | Average Time (hours) |
---|---|
Chassis & Suspension Setup | 40 - 70 |
Body Fitting & Alignment | 50 - 80 |
Engine/Transmission Install | 30 - 50 |
Wiring & Plumbing | 60 - 90 |
Paint & Final Assembly | 50 - 100 |
There's no sugarcoating it: mistakes happen, tools break, parts go missing, and sometimes you need to step away before you throw a wrench across the garage. But you’ll learn a lot, and if you stick with it, you end up with a car that’s totally your own, from the ground up.
Tools, Skills, and Setup You Really Need
Here’s where things get real: not every garage is set up for a full-blown kit car project, and not everyone has the right skills from the jump. Let’s break down what actually comes in handy, so you don’t waste time or money.
Most kits aren’t plug-and-play. We’re talking about mechanical work (suspension, brakes, steering), body panels, and sometimes even full rewiring jobs. If you’ve barely touched a socket wrench, this build is going to force you to learn, fast. People who’ve restored a car, built engines, or handled basic MIG welding find the process a lot smoother.
"Building a kit car is equal parts patience, problem-solving, and prep. You can’t fake your way through poor planning—or a lack of tools." — Steve Temple, Editor at Kit Car Builder Magazine
Your basic setup needs a solid work space—at least a single-car garage with good light, reliable power, and plenty of room around the sides. Forget trying this on a gravel driveway or tight apartment lot. Most builders swear by keeping their tools within arm’s reach, and keeping car parts laid out in a logical order. Plastic bins and zip bags labeled for each step will save your sanity down the road.
- Essential tools: Metric and SAE sockets, torque wrench, screwdrivers, pliers, floor jack and jack stands, electric drill & bits, angle grinder, wiring tools, and a comfortable creeper.
- Handy upgrades: Engine hoist (if you’re swapping in a donor), air compressor, rivet gun, bodywork hammers, and plastic trim tools.
- Consumables: Masking tape, zip ties, shrink tubing, anti-seize, and lots of gloves.
People often forget how much time wiring and bodywork can eat up. If you’ve never messed with fiberglass or gelcoat, you’ll probably be sanding and filling for hours to get the panels smooth before paint. Wiring surprises almost everyone, especially if the harness is made for a different engine or needs fiddling. Watch YouTube tutorials or join kit car forums—these communities are gold mines for shortcuts and common mistakes to avoid.
Tool/Setup | Needed? | Extra Tip |
---|---|---|
Impact Wrench | Nice to Have | Speeds up bolt work massively |
Welder | Sometimes | Handy for custom mounts—local shop can help if you don’t weld |
Engine Hoist | If swapping engine | Rent one if you don’t plan more builds |
Workbench | Must Have | Strong enough for heavy parts, not just a card table |
If you’re not comfortable with a skill—maybe you’ve never done brake lines or painted car panels—call in a buddy or hire that step out. Plenty of veteran builders farm out paint or engine turning and focus their labor dollars where they’ll learn the most or get the biggest win. The trick is to know your limits and not get buried by pride. Fail small in your garage before you bet the whole build on something above your skill set.
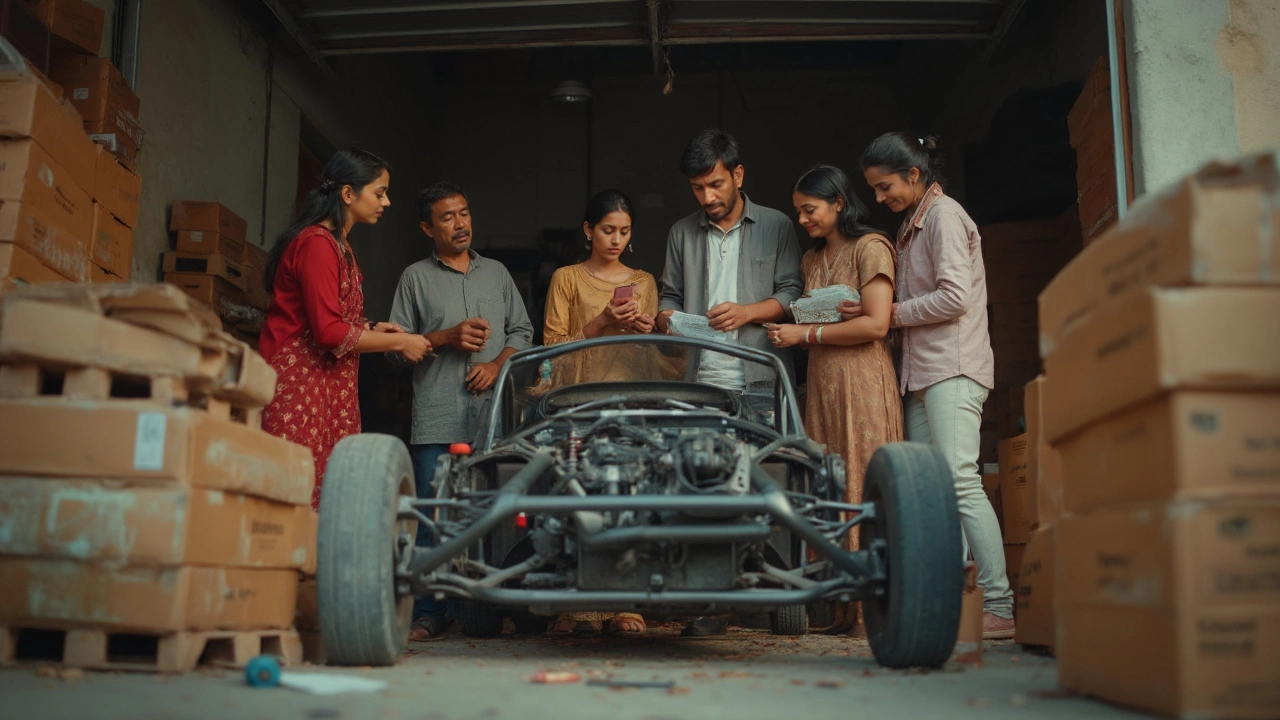
Speed Bumps: Common Problems and How to Dodge Them
Building a kit car sounds like pure fun—until you hit a snag and suddenly you’re googling for hours. Anyone taking on a kit car build is bound to face some classic headaches. Knowing what they are (and how folks get past them) saves a ton of time and frustration.
The biggest culprit? Missing or wrong parts. Even the better kit companies mess up a shipment here and there. Keep your packing list handy and check off parts as soon as your boxes arrive. Don’t start building until you’re sure you’ve got everything—missing something halfway through is a mood killer and leads to way more downtime.
Another regular issue is fitment. Body panels, doors, even the hood—sometimes they just don’t want to line up. Don’t rush the dry fit. Tack panels in place first and walk around the car looking at gaps and lines. Some sanding or even taking a Dremel to a mount is normal—so don’t panic if it’s not plug-and-play.
Wiring hassles are famous. Even with labeled harnesses, diagrams can look like alien language. One smart move is to break it down circuit by circuit—don’t try wiring the whole car in one go. Online builder forums sometimes have color-coded cheatsheets or real photos. Still stuck? Auto electricians are worth their fee—burnt wires are a nightmare.
Then there’s registration and inspection. Plenty of people finish the build, only to get stuck at the DMV because a document is missing or a part number isn’t right. Check your state’s laws before you get too deep—some need regular receipts or original donor VIN plates. Skipping this prep can leave your car parked for months while you sort paperwork.
Problem | DIY Fix | Common Delay (Days) |
---|---|---|
Missing/Wrong Parts | Contact supplier, source locally if quick | 7-30 |
Poor Panel Fitment | Test fit, trim panels, use shims | 3-14 |
Wiring Issues | Tackle one circuit at a time, use test lights | 5-21 |
Registration Problems | Prep paperwork early, contact DMV for requirements | 14-60+ |
One sneaky speed bump? Running out of steam. A shocking number of kit cars never get finished, often just because builders get overwhelmed or bored. Working with a friend, or setting easy mini-goals every weekend, makes finishing way more likely. If you’re stuck, sometimes just changing up tasks (switching from wiring to working on seats) can stop project burnout in its tracks.
Tips to Make the Job Way Easier
Want to build your dream car with less hassle? You don’t need to be an engineer, but skipping rookie mistakes makes any kit car project way smoother. Here’s what helps the most:
- Stay organized from the start. Lay out every part as it arrives and double-check against the kit’s inventory. A simple rolling cart or pegboard turns chaos into order fast—skip digging through boxes every weekend.
- Read the manual front to back before even picking up a wrench. Sounds boring, but you’d be surprised how many folks jump in and get stuck in step three. Some manuals are thick, some not, but knowing the big picture makes a huge difference.
- Invest in basic but good quality tools. Torque wrenches, jack stands, and an electric drill save time. A cheap rivet gun and wire crimpers go a long way for body and wiring jobs. No need for the fanciest stuff, just solid gear you won’t regret.
- Don’t guess—ask. Online forums and builder groups are goldmines for real answers. Builders share what works, and even swap spare parts. Post a photo of a tricky step, and you’ll get quick advice (sometimes within minutes).
- Work in small chunks. Trying to do a major section in one weekend burns out most people. Instead, make a simple checklist for each session. Finish one thing a day and the whole project actually moves forward.
Here’s what catches most beginners by surprise:
Pitfall | How to Beat It |
---|---|
Missing Parts | Check the kit the day it arrives and report anything short immediately. Most companies fix mistakes fast—if you call right away. |
Wiring Trouble | Label all wires as you go. Use colored tape. Snap phone pics before you tidy everything up. |
Running Over Budget | Keep a simple spreadsheet. Add up paint, donor parts, new tools from day one so you don’t get shocked. |
Poor Fit Panels | Test-fit every panel before final drilling. Small tweaks now save big headaches down the line. |
Lack of Motivation | Share progress online or with friends. Seeing feedback and tips keeps you pumped. |
Finally, if you’ve never touched a project this size, start with a buddy who has. Two sets of eyes spot mistakes and lifting a body shell solo is a pain. Take your time, and celebrate every small win—a finished brake line or a perfect door fit is always worth a high five.